Imagine being able to use the dead space in your warehouse to create more usable space for storage, production machinery or even office space. Often called a balcony, mezzanines are situated between the floor and the ceiling. In regards to a theater, the word
mezzanine is used describe the lowest balcony.
Custom Mezzanines
The uses for a mezzanine are many and varied and can be used for most anything requiring extra space and, depending on how much available overhead space you have, it is possible to have multiple mezzanines. Oftentimes a mezzanine will not even require planning permission, especially if the installation is a free-standing unit and using the dead space overhead negates the acquisition of land to expand and the costs of construction. A free-standing structure can also be reconstructed and configured to meet your changing needs. Having a free-standing mezzanine doesn’t mean it cannot pull (or hold) its weight; these systems can meet and/or exceed even military specs. You can design the unit for anything you need and anyway you need it including size, height, flooring materials, landings and stair systems that are made with powder coated steel to resist dings and scratches, therefore, needing less maintenance.
Mezzanine Offices
In some cases, offices are in a separate location than the shop floor on the property and this is often an inconvenient option. There is time wasted traveling between the shop or warehouse to the office and vice versa, and observing daily operations is difficult sometimes. However, if the offices can be located in the warehouse above the production floor, is can be a win-win situation. Workers have better access to office personnel and operations can be monitored right from the offices with no loss of floor space. The mezzanine space can also provide a way to oversee a large manufacturing space with catwalks installed above the floor versus walking up and down the floor. In addition, should you need more office space than a single-story office building can provide, you also have the option of a two story office with steel steps to the second floor. This can be used as plant management offices on the first floor and administration offices on the mezzanine level. Or use a mezzanine to elevate your break or locker room without losing valuable plant floor space.
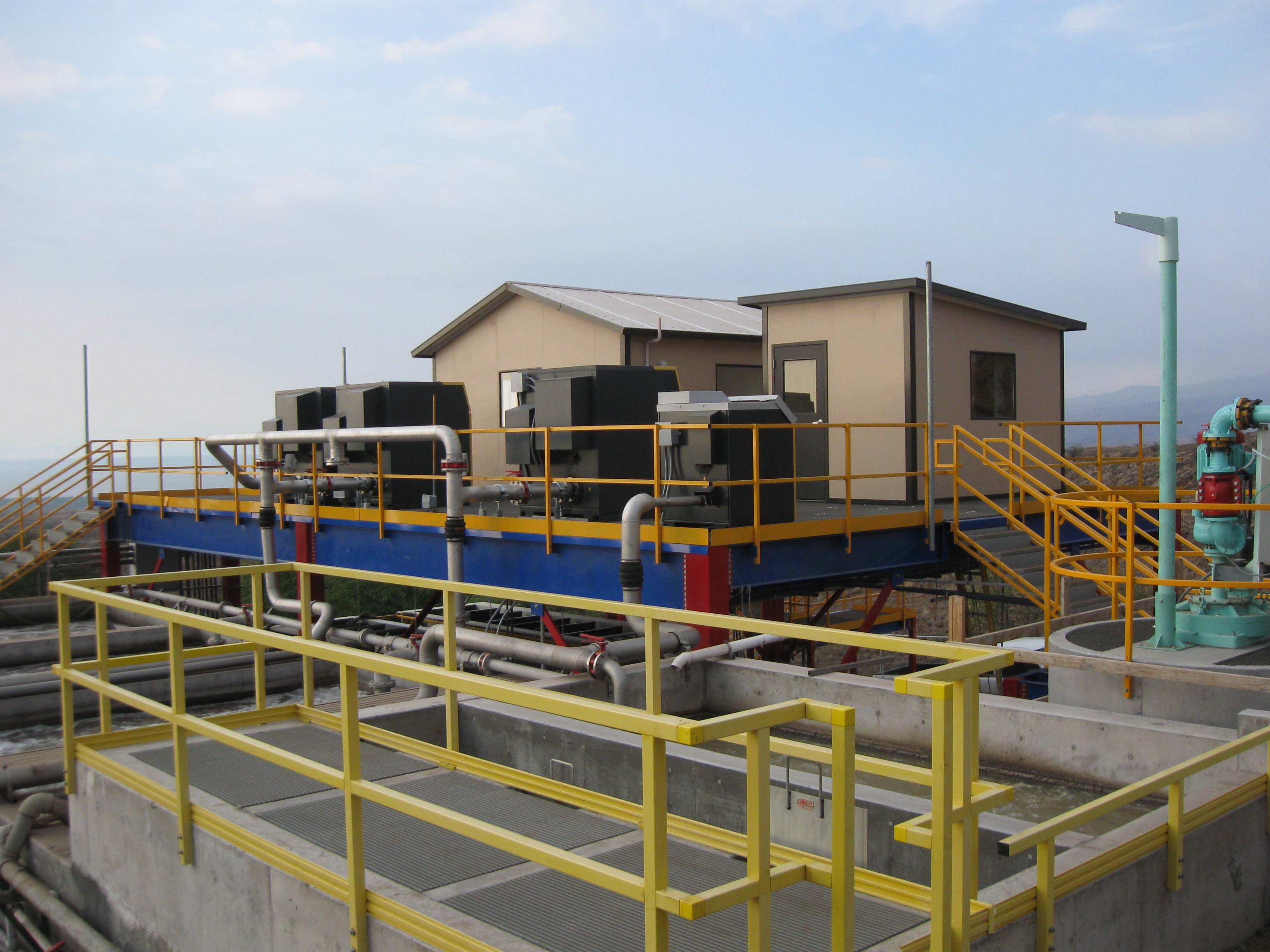
Prefabricated Steel Mezzanines
Prefabrication is the process of building or assembling, in whole or part, sections of a house or other structure, including
modular mezzanines and/or railings and metal stair systems, at the vendor’s factory, transporting to the job site, and installing rather than being built on-site. One of the advantages of this process is a cost saving associated with on-site builds such as delays for weather, materials, or sub-contractors. The climate-controlled atmosphere of a factory allows the build to be worked on rain or shine. The assembly line method of production allows for faster construction and better quality control, which also leads to better quality structures. Installation of a prefabricated structure is up to one-half of the time of traditional build on-site structures which controls costs. It is cheaper to build, therefore, keeping costs down and minimizing lost production time by using bolt together pre-built sections that go up in hours not days or weeks so you keep on schedule. Each pre-built sections bolts together for easy installation. Each product comes standard with free
CAD drawings and instructions that allow each customer to install in-house to save labor, or an installer can be hired.
Mezzanines by Panel Built
Panel Built supplies more than mezzanines; we are an industry leader in this and all fields of prefabricated structures with nearly unlimited uses such as modular classrooms, guard shacks, modular offices, and nearly any building need you have, even an entire industrial complex. Panel Built can even deliver a custom on-site office within standardized specs to your job site in
two business days compete with HVAC! We can supply complete guard and safety rails. We conform to you, not the other way around.
Structural Mezzanines
Of course, manufacturing and other types of plants or warehouses are in no way the only company that needs and utilizes mezzanines. They can be used in any space with the needs that mezzanines can supply. They are used by retail stores, universities, government installations, and distribution facilities. The only limit, of course, the amount of available vertical space, and mezzanines can add a second, third, or more levels. Why not double or triple the usable space? Having more room to grow up not out, may open up a space for new things such as employee break rooms, locker rooms, new production space, stock rooms, and storage to name a few. The custom design means your mezzanine will be arraigned around your existing space as needed, maximizing every square inch available.
Before You Call
In advance of contacting Panel Built (aka Mezzanine Built) consider your needs and your existing structures. Determine where the new space will be in light of the existing equipment and layout of this equipment and anything else in the building where the mezzanine will be located. Decide exactly what the role of the mezzanine will be in regards to storage, offices, etc. Investigate the foundation and whether it will support the new load created by the mezzanine. The standard slab is six inches so it’s important to know if it needs to be reinforced. Evaluate your existing layout and decide where the best place for support columns is and discuss what the best option is for your needs. A mezzanine can substantially increase your usable space. You can double or triple your square footage without building out when you build up.