Sustainable Construction Trends for 2017
In 2016, the construction industry pushed many new boundaries in their sector. With a new focus on technology and safety, the industry made corrections to address two of its biggest issues waste and safety. New and exciting technology first started to get its footing in the industry, like 3D printing and the Internet of Things. After a strong 2014 and 2015, the growth of the construction industry slowed in 2016. However, economists predict a swift uptick in construction spending in the coming year. How will this increase in spending affect the construction industry? How will the construction sector meet the demand for all of these new structures?
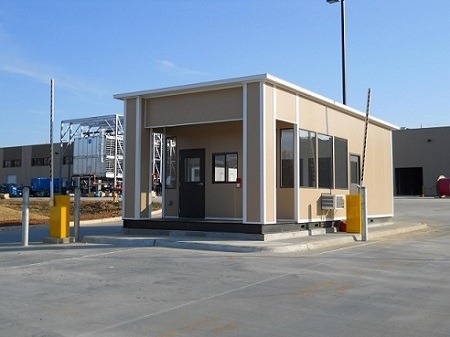
Growing Growth!
As we mentioned before, the construction industry is projected to see a substantial increase in spending over 2017. With confidence in the economy and a sustained revenue flow, companies are more and more likely to invest for the future. With $1,161 billion in construction spending in 2016, we saw an increase of roughly $50 billion from the year. In 2017, the construction sector is projected to have a spending of $1,234.5 billion. This would be almost double the increase from the year before. The rise in spending will be seen across all facets of our economy, with a projected $501 billion coming in the form of residential spending and $732 billion coming in the form of commercial, institutional, industrial, and civil construction. And, perhaps even better the construction industry expects a steady, increasing growth past 2017 as well. Of course, this increase in demand is obviously great for our economy. It shows a confidence in our economic system and country as a whole. In essence, increased spending now will more than likely lead to increased spending in the future. But with this gain, we see an interesting problem in the construction industry. The construction industry is running out of workers to build their structures. One theory is that there is a lack of schools to allow young adults to learn technical skills required for the construction industry. However, many argue that young men and women themselves are moving towards alternative career paths to construction in comparison to the generation before. Like the concept of supply and demand that you learn in a basic econ course, we are seeing the supply of construction labor staying the same or even decreasing while the demand for more construction goes up. This would theoretically lead to an increase in the salary of construction workers and construction companies as a whole, which would, in turn, push more construction workers and firms into the market to enjoy these increased wages. Though, the construction sector has found an alternative to solve this labor problem…
Increasing Use of Modular Construction
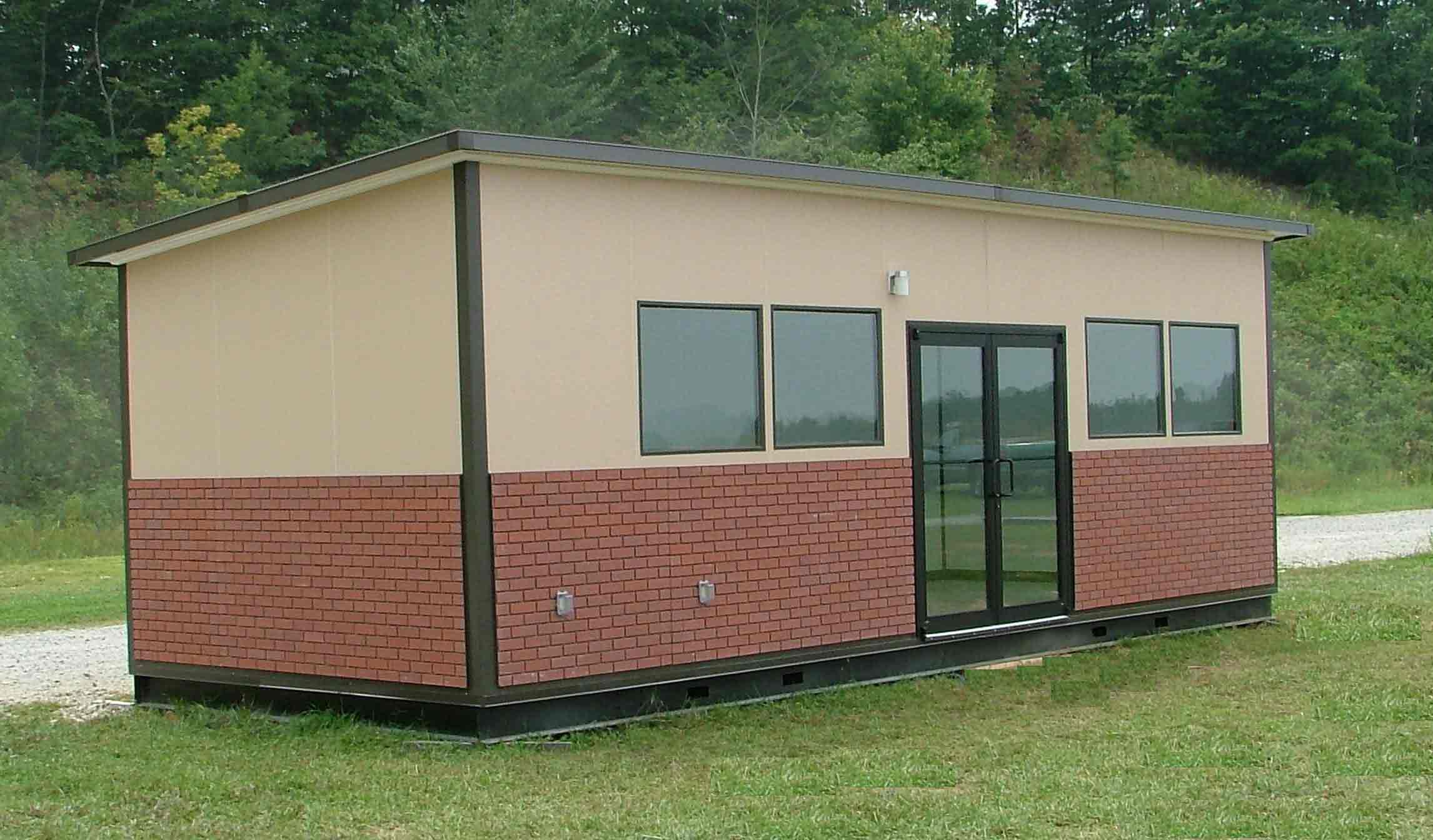
Modular construction solves the construction industries worker shortage in a fairly unique way. Using modular construction times can be reduced by up to 30%-50%. Now, on the surface, this might not seem like a great way to solve labor problem, but shortened project times can have additional benefits beyond just getting things done quickly. Modular construction would allow the same number of workers to complete 1.5 to 2 times the number of projects with their quicker project times. Another issue seen with a reduced construction force occurs in rural areas. The number of quality construction companies in a rural area can sometimes be very low, leaving not a lot of options for a person or company to turn to. But this turns out to be another one of the strengths of modular construction and actually one of the driving factors of its development. As mentioned in our post, “How Modular Construction Works,” the modular construction process was first developed in the 19th century as a way to provide reliable housing to areas with inexperienced or no construction workers. In the past, there has been a bit of an unfair stigma surrounding modular construction. For many, the thought of modular construction conjures up images of “cookie cutter” houses and buildings with little-to-no flexibility in design. Pretty much, “you get what you get.” But today, this is no longer the case. The modular construction industry has completely evolved from its early day. Everything is still constructed off-site, but now all buildings and structures can be completely designed to fit your project and needs. As companies realize the time, money, and struggle that can be saved through the use of modular construction, they will undeniably begin integrating the process into their future building projects, even focusing the developments solely around modular construction.
Marriot just made the switch to modular construction
A Collective Focus on Safety In the construction industry, the standing of the sector hinges on its ability to take care of their workers’ safety. In 2015, 21.4% of work-related deaths came from the construction industry. Due to these alarmingly high numbers, it is in the best interest of the construction industry, construction companies, and the construction workers themselves to do whatever possible to lower these statistics and improve on-site safety. There are many ways the industry has tried to address this issue. With growing applications of technology and the internet of things, companies can completely change different aspects of a construction site. Now, construction workers can wear safety gear that not only protects them from harm physically but also tracks their movement to prevent them from entering hazards in the future. Looking ahead, there are endless applications for this “smart equipment.” Even to the point Similarly, in our last post, “Increasing Site Safety with Modular Construction,” focused exclusively on the role modular construction plays in creating a safer construction site. Particularly with smaller construction companies (accounting for 47% of construction-related fatalities), modular construction can offer a lot to ensure more safety at a construction site. ” Since the structure is indeed a module, workers have one large object to focus solely on rather than many moving parts. For all of the “Fatal Four,” lack of concentration on the hazard proves to be the main cause. With focus centralized on the modular structure, workers can focus on one thing at a time, during the installation of the module. Overall, these pre-assembled structures allow for much lower site disruption.”Construction companies are focusing on this issues for a variety of reasons. First, the companies obviously want to provide safety for their workers. Second, workplace and construction accidents have a drastic effect on the insurance that these companies have to pay to cover their workers. More injuries and accidents = higher cost to the company. Finally, it was being argued that the many hazards of working in construction is one of the main factors driving away potential labor. Many do not want to go through the trouble of learning a skill that is going to directly put them in a hazardous situation. Therefore, people find other lines of work. A focus on safety directly benefits all in the industry, and companies are finding new ways to address this issue.
Green Revolution
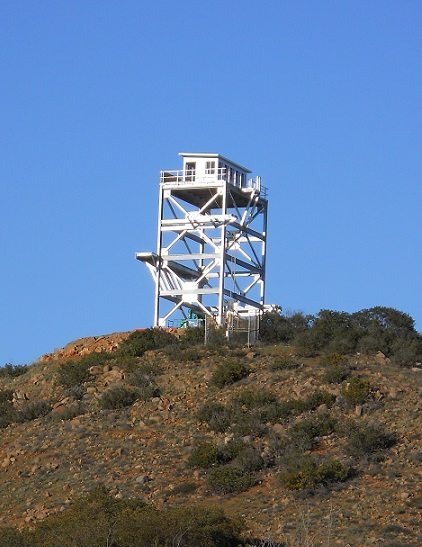
Traditional construction faces many issues when it comes to the handling, creation, and recycling of wasted materials. In fact, an NAHB study found that an estimated 8,000 lbs of waste are created from the construction of a 2,000 square foot building. These squandered materials are all standard materials that you would use to construct a building: wood, brick, insulation, drywall, etc. However, only an estimated 20% of these leftover construction materials are actually re-purposed or recycled, according to The American Institute of Architects. On top of that, the AIA states that “it is estimated that anywhere from 25 to 40 percent of the national solid waste stream is building-related waste.”[1] And in 2009 the Construction Materials Recycling Association, estimated that construction and demolition waste from building construction was around 325 million tons annually. Overall, the integration of the IOT of things will be an asset to help solve construction’s waste problem as well. These items offer instantaneous inventory at all times on the site, helping you use your materials to their fullest ability. Similarly, modular construction’s factory like setting allows for a more orderly work process and standardized materials. Leftover materials are not as much as a problem because they can easily be used on the next project coming down the line. Replacing certain traditionally built buildings with these modular counterparts will help reduce one of construction’s most glaring problems.
Overall, the construction industry will be constantly changing as companies battle it out for projects in this growing sector. Projections are showing a positive trend for 2017 and beyond, and companies will have to adapt in order to meet the increasing demand. Focusing on safety and waste reduction will not only prove to be a positive for the construction industry as a whole but the rest of society as well. If you have any questions about the modular construction process or our company or our modular buildings, give us a call at 800.636.3873 or send us an email at info@panelbuilt.com.