BLOG
Going Lean with Modular Construction
Lean manufacturing has been a goal that companies strive to achieve in order to have their work processes flow as smoothly and efficiently as possible. Everyone has heard of Henry Ford’s use of the assembly line that standardized workflow, streamlined manufacturing, and multiplied production output. Although Ford’s version of lean manufacturing revolutionized the industrial sector and created a new way of thinking in the manufacturing world, it did have one problem, variety! There is a reason why he said, “You can have any color as long as it's black." The Ford assembly line did an amazing job at eliminating wasted material and motion, however it did not allow for customization, making every Model T exactly the same. Today, modular construction involves many different methods similar to Ford’s assembly line but with one enormous difference. Panel Built, Inc. utilizes a process known as mass customization to provide a lean manufactured product that is unique enough to meet our customers’ individual, specific needs. In this post, we are going to establish how our use of modular construction epitomizes lean manufacturing.
To begin, the ultimate goal in lean manufacturing is to constantly achieve the perfect workflow. Also, it’s worth noting that you must “constantly work” for it because many consider an absolutely perfect workflow to be unobtainable, as there is always something you can do better. The best way to imagine this “perfect” process is through this quote from Antoine de Saint-Exupery, "Perfection is achieved not when there is nothing more to add, but when there is nothing left to take away." Oftentimes companies can get carried away, wanting to do more and more things to improve their everyday practices; however, more times than not, the simplest solution is the best. Eventually, you will learn exactly what your work processes look like, and then you can take away any phases that do not directly add value to your product or company. In our modular construction processes, we at Panel Built are constantly working to make our own factory system as streamlined and simple as possible. For example, our prefabricated offices are constructed from two gypsum boards with a polystyrene core. Not too complicated right? Well, each of these panels are constructed on our panel line identical to one another (like Ford’s Model T assembly line). However, our structures have one very important difference that allows us to customize each building for our customers’ specific needs. We employ a binder post system that lets us attach multiple wall panels to one another, forming whatever office size and shape necessary. This manufacturing system is known as mass customization. Taking mass produced wall panels, we can provide a large variety of unique structures tailored to our customer’s exact requirements without adding cost, allowing us to push the savings on to them.
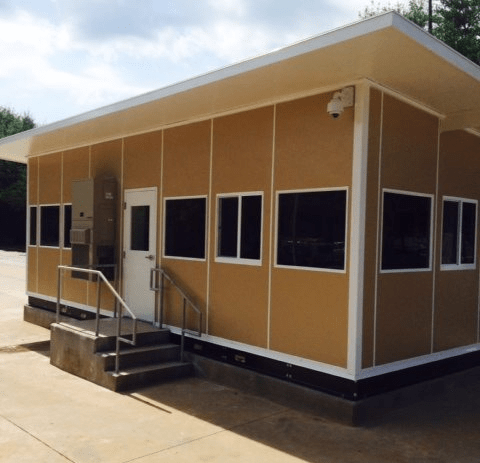
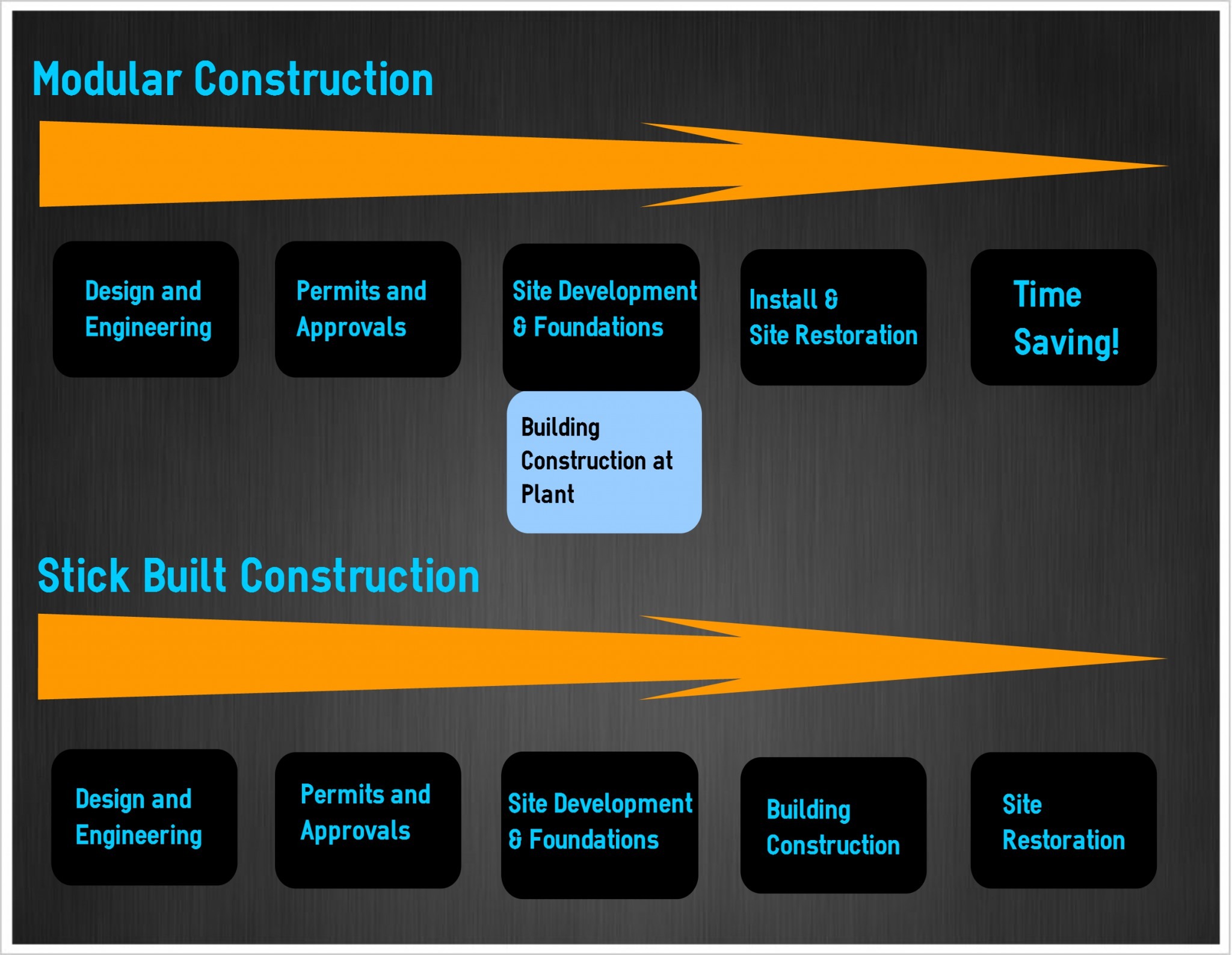
Perhaps the greatest benefit to our lean approach to modular construction is the overall reduction in waste involved. In previous posts, like “Modular Construction: A Greener Way to Build,” we have talked about the stark contrast in the methods of stick-built vs. modular construction. In stick-built building projects an estimated 8,000 lbs. of waste is created from the construction of a 2,000 square foot building and only an estimated 20% of these leftover construction materials are actually re-purposed or recycled. In comparison, using our panelized wall system, any leftover panels can be easily repurposed for another similar job. And since the construction process takes place in a controlled, factory-like environment, there is absolutely minimal chance for any water damage or schedule delays due to inclement weather. Our focus on reducing waste goes beyond just our materials though. We place a continuous emphasis on constantly improving (not adding to) our everyday processes. Rather than making periodically making huge changes, we try to make smaller day-to-day improvements, like slowly chipping away at a piece of granite to make a fantastic work of art. Most importantly, this exercise, known as kaizen, involves all members of our company to collaborate and work together to establish the most efficient workplace possible.
Above all else, we at Panel Built, go through these steps in order to do one thing, deliver the best possible space solution to our customers with excellent service and affordable pricing. When developing a modular project for one of our customers, we take pride in providing them with a quality product that is specifically tailored to their needs; you will not find any cookie cutter modular buildings here. Because, a crucial part of our ongoing lean initiative is provide maximum value to our customers, while producing minimum wasted materials and motion. Panel Built, Inc. has been implementing lean principles into our everyday practices for over 20 years, and we can attribute a great deal of our success to our team’s unwavering support and dedication to this systematic method of eliminating waste.