Modular Construction By The Numbers: What do the Stats Say?
Although modular construction is often thought of as a recent development within the construction industry, it has been in practice for centuries with prefabricated structures and houses dating back to the 17th century. Today, modular construction is used in a variety of different construction projects from hospitals to multi-story apartment towers to correctional facilities. More and more construction teams are electing to use modular methods in the projects because of the many distinct advantages it provides compared to stick-built.
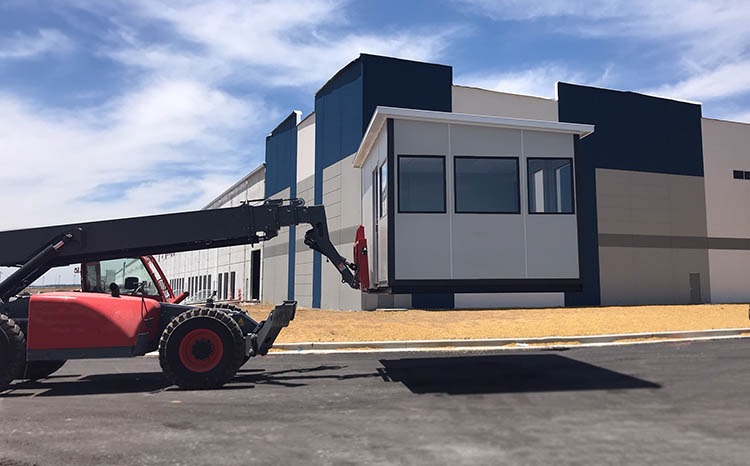
In some cases, these are buildings that must be erected as quickly as possible. For example, we are likely all familiar with the hospital built in China to treat COVID-19 patients. The project utilized prefabricated structures to assemble the two-story building in nearly 10 days! With the building's plans based on an existing facility, the modular construction method allowed for the building's foundation and 'modules' to be formed at the same time. These measures created 1000 new patient beds, 30 different Intensive Care Units, and several isolation wards as quickly as possible.
However, improved productivity is just one of the many reasons that firms are electing to use modular construction in their new building projects. Thanks to one of our favorite organizations, The Modular Building Institute, there's plenty of data available to clearly and accurately show these reasons and how they have improved previous projects. In this blog post, we are going to break down the Numbers & Statistics that go along with modular construction's many other benefits!
79%, 69%, & 53%
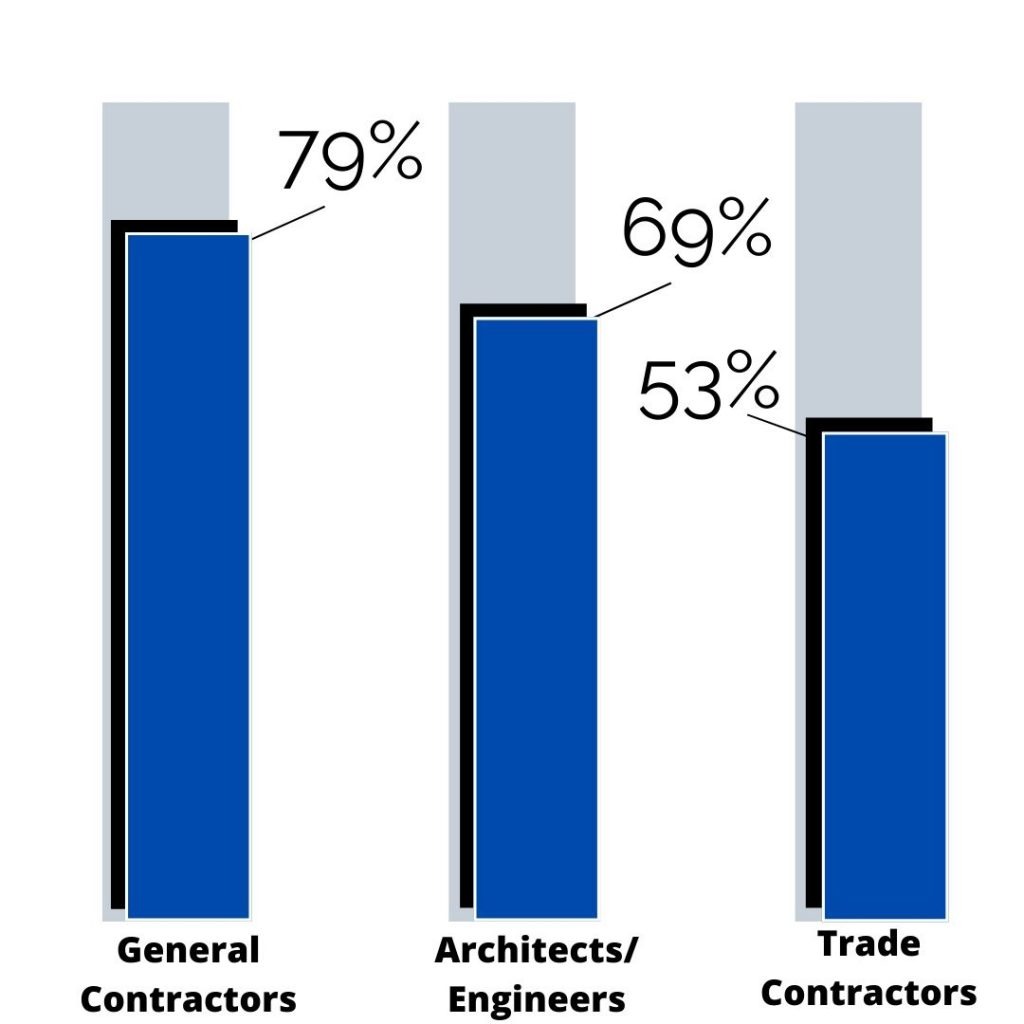
79% of General Contractors, 69% of Architects/Engineers, and 53% of Trade Contractors plan on utilizing a "relocatable modular structure" in at least one of their projects within the next three years. These are specific structures that are "designed to be reused or repurposed multiple times and transported to different building sites," which includes a number of Panel Built's products. Of these three groups, General Contractors predict having the most number of projects with relocatable modular structures with 22% of GCs surveyed predicting over half of their projects will include them in some form. Although only 53% of trade contractors surveyed predicted using a relocatable modular structure within the next three years, 23% of them expected to use one in most of their projects!
Perhaps the most promising note is that Architects/Engineers show a 4.55% increase in firms using the structures, while General Contractors show an 11.3% increase in firms over the next three years. Trade Contractors showed a slight decrease in the total percentage of firms using relocatable modular structures from 61% to 53%. However, the decrease only occurred in firms that were using modular structures in 25% or less percent of projects. Usage stayed the same for firms using relocatable modular structures in more than 25% of projects.
138,000,000 Tons
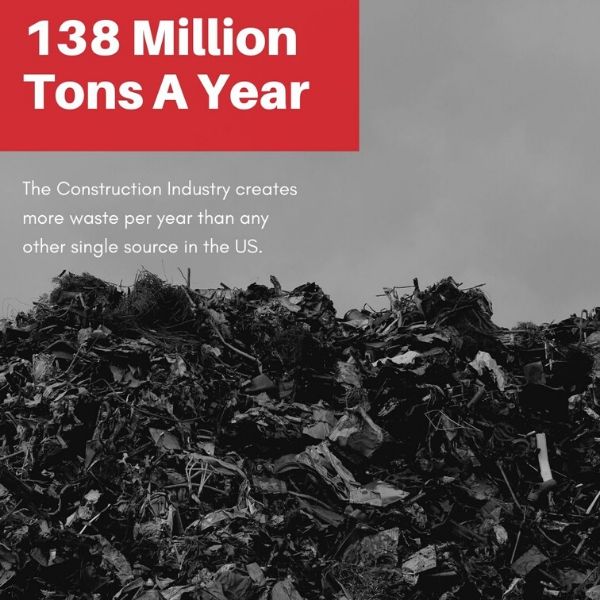
In the year 2015 alone, the Environmental Protection Agency estimates that 138 Million Tons of Construction and demolition materials ended up in U.S. landfills. The construction industry is the single largest source of waste in the United States with four pounds of waste generated per square foot of new building area.
As an inherently green building method, modular construction presents an alternative to stick-built construction to help construction projects reduce the amount of total waste produced. Created in a manufacturing environment, modular structures are frequently fabricated in an assembly line style process. For example, Panel Built's pre-assembled buildings utilize a panelized building method with the panels and extrusions all formed from similar building materials. Any unused materials at the end of one project can be utilized in the next building coming down the assembly line. And for Panel Built's knock-down, panelized buildings, the structures can be uninstalled and reused in another area, rather than being demolished and creating waste.
Using a repetitive building method in controlled conditions allows for modular builders to have a greater control on the quality of their structures as well. Fabricating their modules within a controlled facility means there is a reduced risk of losing materials due to inclement weather. Plus, keeping and story materials in a consistent space means less materials will be lost due to being misplaced or mismanaged. This reduces the amount of construction waste as a whole and the amount of waste seen at the job site, making for a swifter and easier project installation.
71.4%
According to the National Institute of Building Science, 71.4% of firms that committed to a modular construction project saw a noticeable difference in Schedule Advantages/Speed to Market. (The 2015 Permanent Modular Construction: Process Practice Performance survey reported an average of 45% savings in the overall schedule.) And what any business owner will tell you, the quicker you can get a return on your investment the better, allowing you to move on to other projects and continue to earn money. Additionally, 46.4% saw a benefit in the overall quality of construction, and 42.9% saw a benefit in the cost-effectiveness of the project.
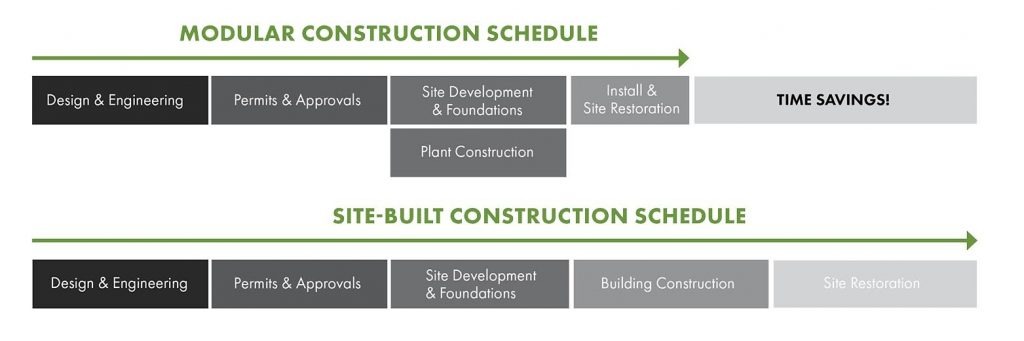
Modular Construction Schedule Diagram Via The Modular Building Institute
The increased speed of modular construction makes it the ideal construction method for sectors and communities in dire need of new buildings. Like the hospital mentioned in the intro, modular construction can be a great tool to use in times of crisis. This need for quick building extends far beyond that of the medical field. Architects and engineers planning public buildings, retail stores, dormitories, hotels/motels, and school systems are looking towards prefabricated solutions more often for future projects within the next three years (according to Dodge Data & Analytics 2020).
$5.81/ Sq. Ft & $10.93/ Sq. Ft.
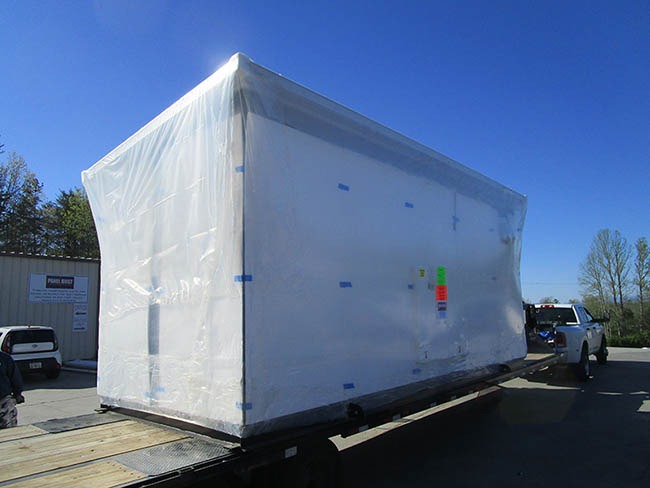
According to the 2015 Permanent Modular Construction | Process Practice Performance's survey analysis, modular construction projects which were able to offer at least a 25% reduction in schedule resulted in an average of $5.81 per square foot of cost savings. Those projects that were able to reduce schedule by 50% or more showed an average of $10.93 per square foot of cost savings. Essentially, what these numbers survey results show is that shortening the project timeline alone helps to keep the overall project costs lower. Workers spend less time on the project overall, leading to lower labor costs. Equipment rentals costs are also reduced with shorter project times, and if the company owns there own equipment, the short modular construction timelines ahllow the machinery to be used much more effeciently and on more projects.
McGraw Hill's SmartMarket Report Prefabrication and Modularization: Increasing Productivity in the Construction Industry, reported that the three Main Drivers for contractors selecting Prefabricated & Modularization in the Projects are: Improved Productivity (92%), Competitive Advantage (85%), and Generating Greater ROI (85%). Many of the contractors that have used modular and prefabricated construction see the methods as a very efficient use of their time. Projects get completed faster, leading to a faster return on their investment, and from there, they are able to move onto more projects, ultimately leading to more revenue in a shorter period of time.
These numbers and statistics highlight some of the many ways Panel Built's modular structures can help you complete your next project as quickly and efficiently as possible. Although we're known for our Modular Offices, Mezzanines, and Guard Booths, Panel Built designs and manufactures a large variety of interior and exterior prefabricated structures, including CMM Rooms, Entry Vestibules, Cleanrooms, Machine Enclosures, Pump Houses, SCIFs, Towers, Trailer Mounted Buildings, and More! No matter what your project, we will adapt our modular systems to fit your needs. If you have a question about our modular structures or would like to get a modular construction quote of your own, give us a call at 800.636.3873, send us an email to info@panelbuilt.com, or ask us in our LiveChat feature in the bottom-right of the page. We're always happy to answer any questions or concerns that you may have.
Sources:
https://www.modular.org/documents/public/PrefabModularSmartMarketReport2020.pdf
https://cdn.ymaws.com/www.nibs.org/resource/resmgr/oscc/oscc-2018surveyreport.pdf
https://www.modular.org/documents/document_publication/national-crisis-looming-whitepaper.pdf
https://www.nist.gov/system/files/documents/el/economics/Prefabrication-Modularization-in-the-Construction-Industry-SMR-2011R.pdf